TOP > ASEAN便り > もはや待ったなし。開発設計部門は今すぐIoT/ICTで開発プロセス革新を!
もはや待ったなし。開発設計部門は今すぐIoT/ICTで開発プロセス革新を!
2018年1月10日
〜コンカレント・エンジニアリングの進化から見えてきた
業務革新のカギとは〜
今回はものづくりにおける設計・開発の「革新」について、これまでの経緯などを振り返りつつ、私なりの処方箋(ヒント)を提示してみようと思います。
日本企業の設計・開発部門が置かれている環境は、ますます厳しくなっているということは、誰もが認めることだと思います。顧客ニーズが多様化して、さらに開発期間も短縮させられるとなれば、十分な技術検討ができなくなり、実際に品質にしわ寄せが来ています。
一方で、開発規模の増大で拠点間の開発・製造、国内外へのアウトソースによる分業が加速するにつれ、設計力や生産技術力が低下し、製品やシステムの全体を把握できなくなって設計のモレ、評価項目モレが多発しています。
こうした状態でも製品数は増加し、しかも生産性も上げなければならいのです。当然ながら情報共有が追いつかず、多くの製品で類似品質トラブルが発生しているようです。
また、工場が海外へとシフトすれば海外拠点とのやりとりも増え、移転ともなれば生産技術や購買の業務も担当するなど技術者の仕事範囲も拡大し、「純設計工数」をなかなか確保できないという問題もあります。となれば、自社の技術やリソースだけでは限界だということで、アライアンスやアウトソースを進めても、これまで垂直統合に慣れていた業務スタイルから脱皮できず、少しも状況が好転しないというケースが見受けられます。「負のスパイラル」に陥っている企業が少なくないのです。
コンカレント・エンジニアリングから開発プロセス革新のエッセンスを知る
「負のスパイラル」から脱却するためには、改めて基礎技術スキルの向上、基礎マネジメント力の向上を図る取組みが必要になります。しかし、多忙を理由に人材育成を怠り、今までどおりの業務スタイルを継続してはいないでしょうか。このままでは品質トラブル対策に追われ、開発プロセスがますます「重いたい業務」になってしましいます。
近年は、こうした状況に陥っている企業によく出会います。現場の現状を踏まえつつ開発プロセス革新に取り組むべきだと改めて感じています。これまでの開発プロセス革新を振り返ると、コンカレント・エンジニアリング(Concurrent Engineering)の導入・展開が大きく影響しています。コンカレント・エンジニアリング(以下、CE)は、アメリカの国防総省が30年ほど前に提唱したもので、開発プロセスを同時並行で進めるための調査研究がもとになっています。日本では自動車や電機系の企業が開発プロセスのフロントローディング化への志向が強く、開発プロセス革新活動にCEを導入するようになったのです。
先に話したように、今日までに開発設計、製造部門を取り巻く環境は劇的に変化しました。日本企業の得意なすり合わせ、垂直統合だけでは勝負できないのです。世界的には水平統合、オープン・イノベーションを取り入れたCEの取組みがすでに始まっています。CEそのものも進化しているのです。
私の感覚では、提唱されて導入され出した段階でのCEをCE1.0とでも名づけるとすれば、今はCE4.0ぐらいまでにバージョンアップしていると思います(下図)。ただし、1.0や2.0ではダメだということではなく、自社を取り巻く環境や現場の状況に適したバージョンの選択が重要だということに注意してください。
CEの進化の過程は開発プロセス革新の変遷と密接に関連していますから、ここでざっとその進化を振り返ってみましょう。
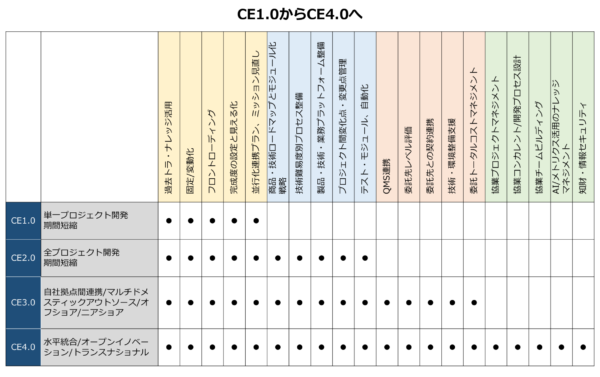
コンカレント・エンジニアリング初期(CE1.0)
CEはアメリカ・日本・ヨーロッパの200社あまりの企業を比較調査の結果から作成した政策提言をベースにして、日本型の開発期間短縮のアプローチを系統的に整理したものとも言われています。日本企業はCEを「逆輸入」して各社なりに工夫して導入したということです。
日本の製造業では、研究開発・設計と製造工場が別組織になっている場合が多いですし、そうなると取締役レベルから完全に分かれ、物理的にも拠点が離れていることが多いのです。給与形態に合わせ、最近は別会社になっていることも多くなっています。また、製造工場1社ですべてを賄うのではなく、多くの協力工場や関連企業に分散されています。こうした状況でCEに求められるのは、物理的にも組織的にも離れている組織を有機的に連携させ、並行化プロセスを描いて開発期間を短縮することです。
ですから、初期のCE(CE1.0)の導入は、これまでの組織ミッションを超えた活動が求められたため、ある特定プロジェクトを選定し、そのプロジェクトでさまざまなトライを行うという形で進んでいったのです。
しかし、組織ミッションの解釈や実践に成熟していない状態でCEを導入することもあって、推進するうえでさまざまな課題が指摘されました。要するに組織の壁をなくして組織間でシナジー生むプロセスをいかに構築するかということです。たとえば、生産技術・製造・品質保証部門などは下流のプロセス段階で発生した問題を処理するのではなく、上流の開発設計部門と協力して後工程で想定される問題を洗い出し(フロントローディング)して、開発工程の「手戻り」を削減しなければなりません。これはCEの基本中の基本です。そのための提案ができるか、それらを踏まえた並行化プロセスを描けるか、実際にそれを実行できるか、などの課題です。
CE1.0を効果的に実現している事例は、自動車業界に多く見られます。こうした多くの事例から、CE1.0の実効性を高めるための5つの原則を抽出することができました。機会があれば詳しく説明しますが、かいつまんで話しておきましょう。
原則1としてまず言いたいのが、「過去のトラブルを分析して課題を明確にする」ことです。これらをナレッジ情報として次の開発へのフィードバックポイントにしておきます。要は失敗に学ぶ、同じ過ちを繰り返さないということです。
原則2は「設計内容を固定部と変動部(基本仕様とオプション)に分ける」ことです。固定部と変動部の設計方針を明確にして、それぞれに活用すべき技術を評価するのです。既存技術の流用などで設計効率の向上が図れます。
そして原則3は「フロントローディングを定着させる」ことです。これはあらゆるCEの基本でもあります。源流段階での課題の洗い出しで、事後の課題解決を極力なくすのです。事後対応が増えるとプロセスを並行に進めるのが難しくなりますからね。
原則4はCEに限ったことではないのですが、「ステージターゲットで完成度を設定して見える化する」ことです。進捗を管理するのではなく、完成に至るまでの課題を管理するのです。
最後に原則5として「並行化した業務のプラン・ミッションを見直す」ことです。与えられたことをそのまま受け入れるのではなく、マネジャーや他部門も巻き込みながら、臨機応変に働きかけることも重要です。
コンカレント・エンジニアリング中期前半(CE2.0)
CEの導入が進み成果も出始めると、選定されたモデルプロジェクトだけでは満足できなくなります。当然ながら全商品の開発にCEの導入を加速させたいということになります。こうした動きに対応したのがCE2.0だったと言えます。
全プロジェクトに導入するには、生産技術、製造、品質保証部門といった下流工程がますます重要になってきます。これらの部門はルーチンの製造による製品対応の業務がメインですから、新商品開発に対応した業務が増えるとなるとリソースの分担と体制の構築が必要となります。また、新商品開発に対応するには製品がまだない状態でも上流部門に課題やリスクを指摘できるスキルが必要で、そのスキルを持っている人材に業務負荷が集中してしまうのです。部門として人材育成をしっかりやらなければならないわけです。全プロジェクトとなれば関わる人も増えるため、人材育成は避けて通れないのです。
またCE2.0では複数の商品を効果的に開発設計してくわけですから、モジュール化やプラットフォーム整備も必要になります。さらに、これらを効果的にマネジメントするためには商品・技術のロードマップをつくらなければなりません。中長期的な商品投入計画と技術開発計画、モジュールやプラットフォームの適用計画などが示されたロードマップがあれば、リソースの投入・配置計画と人材育成計画を効果的に進めることができるのです。
コンカレント・エンジニアリング中期後半(CE3.0)
2000年代に入り、エレクトロニクス業界ではデジタル化が進みました。その一方で、新興国のベンダーの製品と機能の差別化が難しくなり、コスト競争に突入していったのです。こうなると、もはや部品コストだけでは勝負できません。開発費に占める人件費や製造の組立・加工費のコストダウンが叫ばれ、開発設計や製造の新興国へのアウトソースが加速していきました。オフショア(ソフトウェア開発の海外アウトソース)やODM(Original Design Manufacturer:開発設計の委託)、EMS(Electric Manufacturing Service:製造の委託)が身近に感じられるようになったのもこのころです。
アウトソースをベースにするCEの導入・推進にあたっては、委託コストとマネジメントコストの両輪を検討することがポイントとなります。これはCE3.0の段階であると言えます。
たとえ委託コストが安くても、先方のスキル不足などで品質トラブルが続出するようでは、自社側でのマネジメントコストが増大してしまいます。マネジメントを効果的に実施するには、委託先の品質マネジメントシステム(QMS)、保有スキルを正しく理解したうえで連携する必要があります。連携となると技術資産や設計ツールの提供も積極的に求められので、技術流出を気にする風潮もあるかもしれません。しかし、自社のコア価値を明確しておけば、提供できる資産も多数あるはずであるし、V字的アプローチによる受入れ評価項目の先行提示も品質向上に寄与するはずです。
技術流出や品質トラブル続出による日程遅延、マネジメントコストの増大については、ペナルティも考慮して契約することが大切です。一方で、委託先のモチベーションを上げるためにも、成功したときインセンティブもきちんと検討して契約しなければなりません。
最近のコンカレント・エンジニアリング(CE4.0)
日本の市場もすっかり飽和気味です。機能の差別化だけでは話になりません。新商品開発、開発設計の重要なキーワードを思いつくまま列挙してみると、「製品+サービス」「グローバル対応」「自社にない技術の取り入れ・協業/オープン・イノベーション」「技術起点/技術者からの先行提案」などでしょうか。
これらのキーワードから導き出されるのは、協業先(オープン・イノベーション、サプライヤーなど)、社内サービス部門、市場・顧客とで定常的にシームレスな連携を実現するコンカレント体制の構築が求められているということです。
CE3.0までは、どちらかというと社内中心の活動になりがちでしたが、何とかさまざまな課題をクリアしてきました。これからは(CE4.0では)、社外と積極的に「コンカレント」(一致した協業)を進めなければなりません。視点が社内に向いている企業にとっては、何をするにもハードルが高くなると思います。もちろん、協業先は日本企業だけではありません。むしろ海外企業が増えてくるはずです。日本人に求められるマネジメント・スキルセットを習得するためのハードルの確実に上がるはずです。たとえば、協業プロジェクトマネジメント、協業コンカレント、協業チームビルディング、AI/メトリクスを活用したナレッジ・マネジメント、知財・情報セキュリティは必須です。言葉を聞いただけでもハードルが高そうですが、これらは海外企業と仕事をする際にとくに重要になります(下図)。
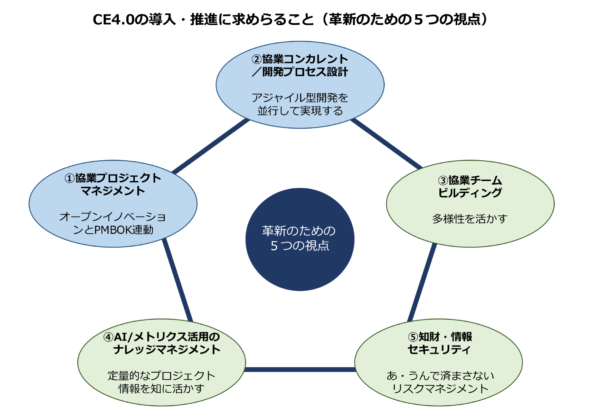
IoT/ICTの積極導入で技術者自身が積極的に改革に取り組むべき
先に話したように、もともとCEは日本がイケイケドンドンで成長していた時代の仕事のやり方を整理・体系化して生まれた考え方です。時代とともに環境は変わります。時代が要求するさまざまな課題に合わせ、アプローチも変化させていかねければなりません。
今は新興国企業のレベルアップと追い上げが激しく、日本の製造業も岐路に立たされています。過剰品質、コスト高、技術者の高齢化の加速、製造工場の新興国移転に伴う技術力の低下、学生の理系離れなど、ものづくりにとって明るい情報はなかなか聞こえてきません。だからこそ今、日本企業に求められるのは、業務革新・働き方改革で価値ある業務にフォーカスすること、市場・顧客を徹底研究して価値ある製品・サービス・ソリューションを届けること、セクショナリズムにとらわれずに業務分担を見直すこと、そして何よりも技術者自身がそのような取組みを積極的に進めることです。
幸い、IoT/ICT環境は劇的に変化しています。開発設計部門もそれらの活用で業務革新ができるチャンスが到来していると言えます。IoT/ICTで情報のインプットやアウトプット、関連する情報のリアルタイムでの確認をまるでコックピットにいながらにして可能になるような環境があれば、多人数による「すり合わせ開発」から少人数による「セル開発」への移行も不可能ではないです。少人数でのセル開発が進めば、多人数でのデザイン・レビューや評価なども省略できると思います。「重たい業務」から解放されれば、価値ある業務に工数を投入できるというわけです。
製造工場ではIoTは積極的に導入されつつあるようですが、開発設計部門での導入まだまだ課題が多いのも事実です。しかし、IoT/ICTを積極的に活用していくことにチャレンジすべきです。また、他業種のICT活用を学ぶことで、自社の開発設計プロセス革新へのヒントが見えてくることがあります。
最後に少し細かい資料ですが、開発設計プロセス全般にわたってIoT/ICT/CAEの導入を検討するときに使えるチャートを紹介しておきます(下図)。CE4.0時代をチャンスと捉え、開発設計の仕事のやり方をぜひ革新していていきたいですね。
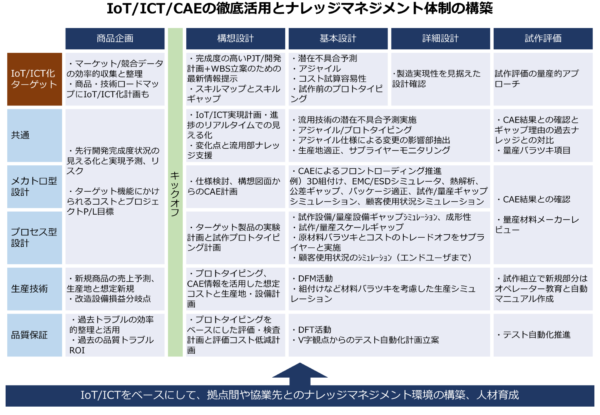
なかなか「ハードルが高い」と悩まれているようでしたら、ぜひJMACにご相談ください。超えるべきハードル自体は下がりませんが、みなさんのスキルセットの向上はしっかりと支援いたします。